Association for Craft Producers (ACP), a non-profit and a non-government fair trade organization. ACP was incepted in 1984 to provide regular design expertise, technical assistance, management as well as marketing to low-income craft producers in general and women craft producers in particular which results in regular adequate wages to supplement the family income and improve the overall standard of living.
One of the major objectives of the association is to provide a safe, clean and productive work environment as well as to protect the environmental and natural resources and the locations where we operate. The Corporate Creed includes the pledges to ” Protect the environment and natural resources in the locations where we operate to preserve them for the benefit of the communities we serve and for the future generation”. ACP has always had Environmental concerns. We are committed to undertaking precautionary measures to prevent industrial pollution. For the preservation of Nepal’s fragile environment, ACP has taken various steps in its production processes.
Smoke-Free Environment:
Taking into consideration the hazardous effect smoking has on the health of individuals as well as polluting the air, ACP discourages smoking. The producer and staff code of conduct strictly prohibits smoking inside the premises of the Association.
Wastewater Treatment Plant:
The production of handicrafts is done either in the ACP workshop or at the producers’ own homes. In the workshop in Kalimati, numerous activities are executed from which printing and dyeing activities generate toxic wastewater. The source of wastewater at ACP is the block printing unit, screen printing unit and dyeing unit. From the printing unit, mainly cleaning of the equipment generate wastewater while from the dyeing unit, the wastewater exists from different dyeing baths. The wastewater contains a lot of chemicals like dyes, bleaching powder, emulsifiers, binders, acids, salt etc. In 1994 with the help of a consultant from UNIDO, a simple effluent treatment plant was constructed.
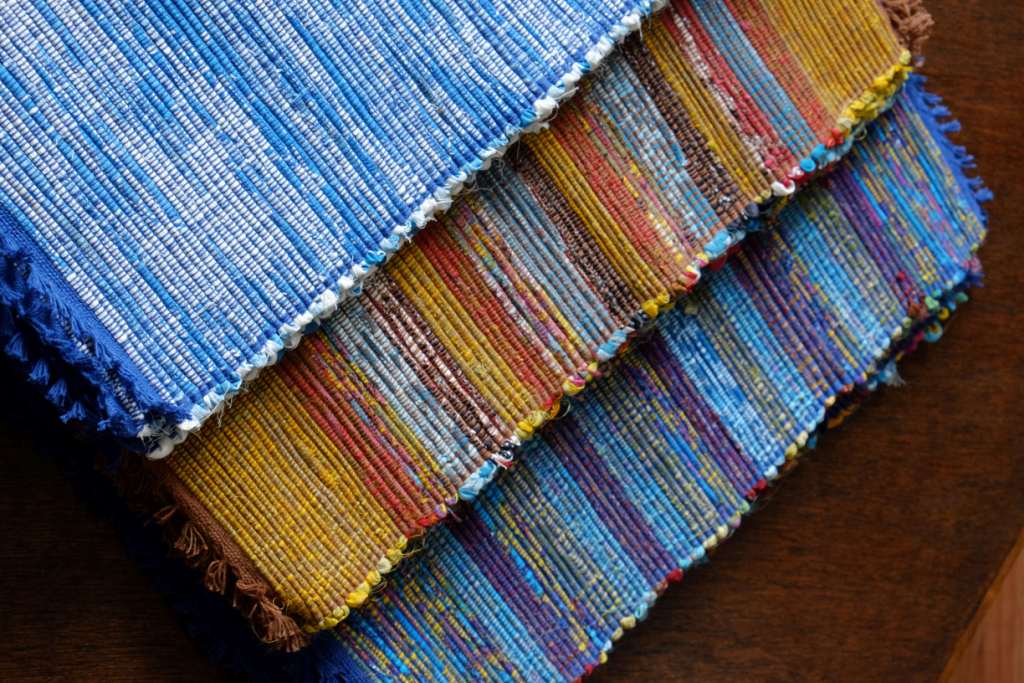
Due to the increased activities of the Association, more advanced dyeing equipment was installed which resulted in an increased amount of waste water. Because of this transformation, the water treatment system established in 1994 did not meet the requirement. In 1997 with the support of SNV, an improved treatment plant was constructed. This treatment system has a treatment capacity of 15,000 litres/ day compared to 7000 litres/ day of the previous treatment system. In 2005, the cotton dyeing and processing unit of ACP was upgraded. This upgradation has increased the capacity of the dyeing unit which would also generate more waste water. Thus to accommodate this additional waste additional water treatment tank has been constructed.
Rainwater Catchment System:
Water consumption of the organization is very high. 75% of the water is used for dyeing and washing purpose. Taking into consideration the scarcity of water in Kathmandu, the Association installed a rainwater catchment system. A gutter had been affixed to the roof area of 3888 square feet. During the rainy season, water was collected in the underground tank with a capacity of 20,000 litres.
In 2005 as a part of an expansion of the cotton dyeing and processing unit, we dismantled the old collection tank and built a new underground rainwater collection tank with the capacity to collect 300,000 litres of water. Rainwater is collected and used for washing and dyeing purposes.
Changeover from kerosene-based firing to electric firing:
In 2016 ACP installed a 32kWp solar plant on its premises. We have also installed a 4.96 kW solar system in our real store and solar water preheating system for our dyeing unit. This has largely contributed to self-reliance in energy.
· Product Development/ upcycling: product developments are being done using waste/ old materials e.g.- recycle yarn, silk sarees, scrap cotton fabric, and glass bottles. Recycled paper is used largely in producing paper products.
· Harnessing of steam: The steam released during the cooling off of the boilers in the dyeing unit is used to heat the water required for the felting.
· Changeover from kerosene based to water-based printing inks and substituted acetic acid with hydrochloric acid: We have substituted kerosene-based dye with water-based dyes. This has reduced the pollutant in the wastewater.
· Use of sustainable and biodegradable raw materials like clay, softwood, cotton, bamboo, wool and recycled paper.
Shared by : Revita Association for Craft Producers Nepal